What is Composite Cladding?
Aluminum composite panel curtain wall is a modern facade cladding system that combines aesthetics and functionality, mounted on the exterior surfaces of buildings. This system typically utilizes aluminum composite panels made of a thermoplastic polymer material, such as polyethylene, sandwiched between two aluminum sheets.
Features of Composite Curtain Walls
- Multi-Layered Structure: Created by sandwiching polyethylene or another thermoplastic material between two aluminum sheets.
- Flexible Design: Available in various colors, textures, and shapes.
- Smooth Surface: Composite panels feature a flat and smooth surface.
- Lightweight: ACPs are an exceptionally lightweight material.
- High Durability: Resistant to UV rays, abrasive substances, corrosion, and other external factors.
Advantages of Composite Panels:
- Aesthetics: Provides a modern, sleek, and stylish appearance.
- Durability: Resistant to extreme weather conditions, corrosion, and UV rays.
- Lightweight: Its lightweight structure does not add extra load to the building.
- Easy Maintenance: The surface is easy to clean and has low maintenance costs.
- Flexibility: Easily moldable and offers various design options.
- Thermal and Sound Insulation: Provides excellent thermal and sound insulation.
- Cost-Effective: Long-lasting, ensuring cost savings over time.
Disadvantages of Composite Panels:
- Fire Risk: The polyethylene core in some aluminum composite panels can propagate flames in case of fire. However, fire-resistant composite panels are also available in the market.
- High Initial Cost: The initial cost of high-quality composite panels can be higher compared to other cladding options.
- Installation Sensitivity: Improper installation may lead to issues like water leakage or air infiltration.
- Limited Repair Options: Damaged panels are difficult to repair and typically need to be replaced.
Where Are Aluminum Composite Panels Used?
Aluminum composite panels are a preferred material in many structures and applications due to their aesthetic and functional advantages.
Applications of Aluminum Composite Panels
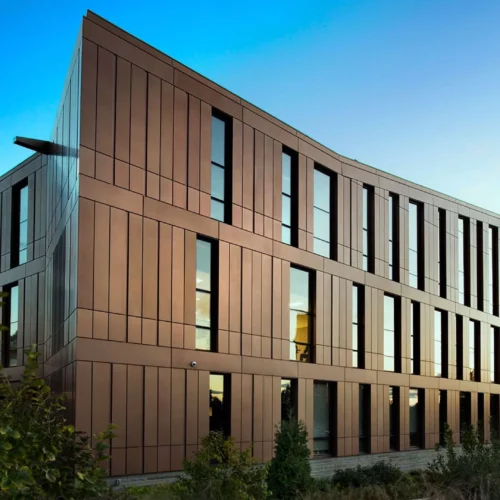
Used on the facades of office buildings, shopping malls, hotels, hospitals, schools, airports, and many other commercial or public structures. It provides a modern and stylish appearance.

Aluminum composite panels are used in lobbies, foyers, conference halls, office interiors, and other indoor applications as wall cladding, ceiling covering, or decorative elements.
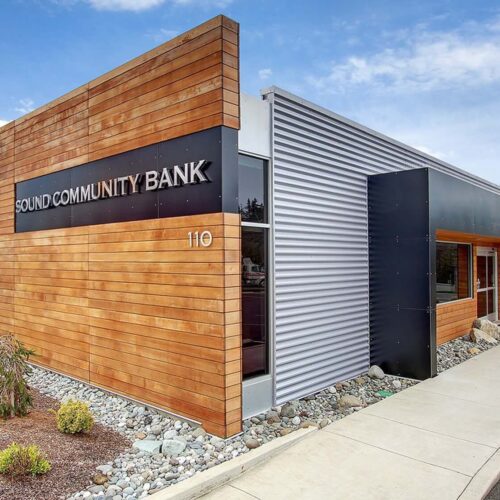
The durability and smooth surface of ACPs make them ideal for large billboards and signage applications.
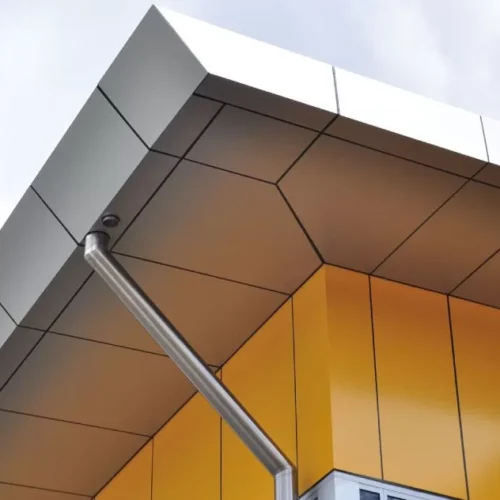
Used for building entrances, window covers, or outdoor seating areas to provide protection from the sun and rain.
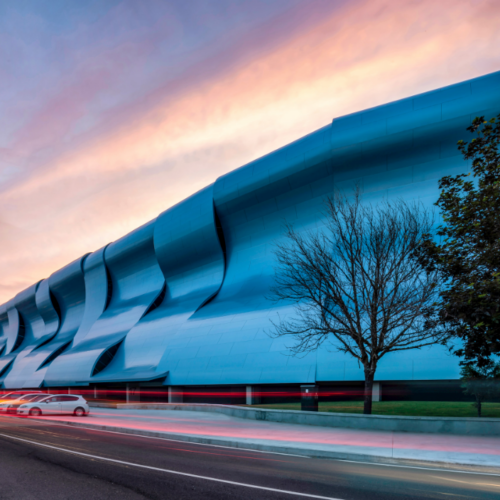
Used in the exterior cladding or interior decoration of modern sports complexes and stadiums.
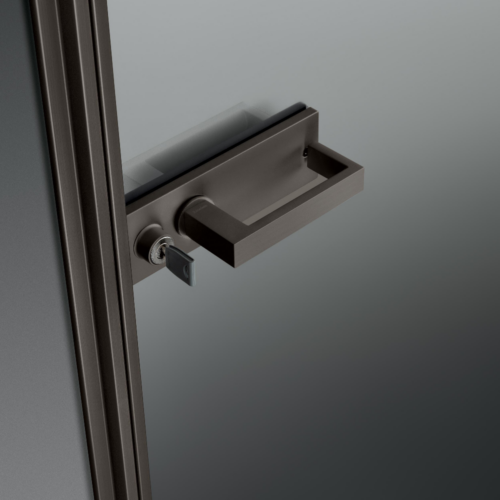
Used within the frames of aluminum doors. Commonly preferred in offices and restrooms.
The wide range of colors, textures, and shapes available for aluminum composite panels offers versatile application possibilities. However, it is crucial to select fire-resistant and high-quality materials based on the intended use.
What Are the Technical Specifications of Aluminum Composite Panels?
Aluminum Composite Panels are manufactured by adding a polyethylene (PE) or mineral filler material between two aluminum sheets.
Technical Specifications of Aluminum Composite Panels
- Composite Panel Weight:
- The typical weight of ACP per square meter ranges from 3.5 kg to 5.5 kg, depending on panel thickness, filler material, and aluminum sheet thickness.
- Composite Panel Dimensions (Sheet Sizes):
- Standard sheet widths: Typically 1,220 mm, 1,250 mm, or 1,500 mm.
- Standard sheet lengths: 2,440 mm, 3,050 mm, 3,200 mm, or longer.
- Some manufacturers also offer custom-sized panels.
- Composite Panel Colors:
- ACP is available in a wide range of colors, including matte, glossy, metallic, wood-grain, marble-patterned, and custom designs. Special colors can also be produced upon request. Access the color chart here.
- Composite Panel Thickness:
- Typically available in 3 mm, 4 mm, and 6 mm thicknesses, but this may vary based on the manufacturer and intended use.
- Composite Panel Fire Ratings:
- Plastic-Filled (PE-Filled) Panels: These panels use a polyethylene core and are generally less resistant to fire.
- Mineral-Filled Panels: These panels are more fire-resistant and are specifically designed to meet certain fire regulations. They contain a mineral-based core material.
The technical specifications of aluminum composite panels may vary depending on the manufacturer, material quality, and the specific requirements of the application site. Therefore, consulting the manufacturer’s technical details is the best approach when selecting the right panel for a specific project.
How Are Aluminum Composite Panels Made?
The manufacturing of composite panels is a highly technical and detailed process. It requires specific machines and methods.
Aluminum Composite Panel Manufacturing

- Raw Material Preparation: Aluminum coils, polyethylene (PE) or mineral fillers, and coloring agents are prepared.
- Extrusion Process: Polyethylene or mineral filler is melted at high temperatures and extruded between two aluminum sheets.
- Cooling and Hardening: The sheets are cooled and hardened before being packaged.
- Surface Treatments: A coating is applied to the sheets to provide the desired color and texture. This coating typically offers corrosion protection.
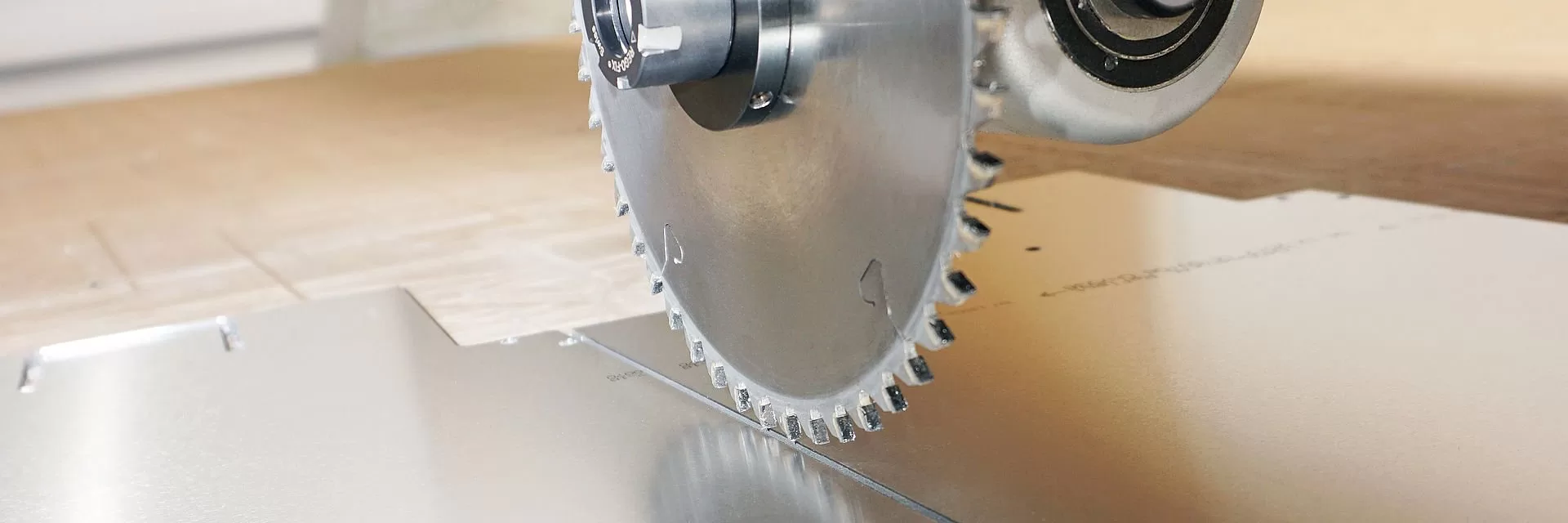
- The cutting dimensions of the panel are determined and precisely cut using cutting machines.
- Cutting is performed at dimensions and angles defined by the project’s requirements. CNC machines are preferred for custom shapes and cuts.

- The grooving process is an application that allows panels to be bent at specific points.
- This process is particularly necessary for corner details, column claddings, or surfaces with special shapes.
- Through grooving, only a specific part of the panel is thinned, enabling easy bending at the grooved area. This allows panels to be installed in the desired shape and form while maintaining their integrity and durability.
How Are Aluminum Composite Panels Installed?
Composite panel installation can vary depending on the structure of the panels, the surface they will be applied to, and the design requirements. Two common installation methods are:
- On steel construction
- Key-lock hanging system
Aluminum Composite Panel Installation
- Steel Construction System:
This method is typically preferred for large facades or high-rise buildings.

- Substructure: A framework made of steel or iron is mounted onto the main wall of the structure. This framework forms the base for installing the composite panels.

- Screwing Process: After special grooving processes are applied to the back of the panel, the panels are mounted onto the framework using screws through these grooves. The screwing process ensures the panel is securely fastened to the framework.
- Key-Lock Hanging System: This method is used particularly for projects requiring fast installation or when an aesthetically pleasing installation is preferred.

- Kompozit Panel Profilleri: Bu sistemde, panelin arka yüzüne monte edilen özel alüminyum profiller kullanılır. Bu profiller, panelin asılacağı ana konstrüksiyonla uyumludur.

- Special Openings on Panels: Special openings are made on the panels for the key-lock hanging system. These openings are where the aluminum profiles will fit through.

- Fitting Panels into the Hanging System: During installation, the openings and profiles interlock like a key-lock system, allowing the panel to be easily mounted.
Both systems offer their own advantages and disadvantages. The steel construction system provides high durability and stability but may require a relatively longer installation process. On the other hand, the key-lock hanging system allows for faster installation but requires careful attention to structural durability needs. The choice of installation method should be determined based on the project’s specifications, budget, and time constraints.
Aluminum Composite Panel Technical Details
Composite Panel Detail
Alüminyum Kompozit Panel Uygulama Detayları
Structural Silicone Curtain Wall Technical Specification
You can access a sample technical specification for composite panel cladding applied by Üçgen Alüminyum here.
Aluminum Composite Curtain Wall Companies
Companies specializing in composite cladding provide solutions that combine aesthetics, durability, and functionality for the facades of modern architectural projects. These firms use materials like aluminum composite panels (ACP) to enhance the appearance and performance of buildings. Such companies typically possess the following characteristics:
- Expertise and Experience: Composite cladding firms work with specialized teams experienced in the manufacturing, design, and installation of aluminum composite panels. Their years of experience help manage projects successfully.
- Product Variety: They offer a wide range of options in terms of colors, textures, patterns, and sizes to meet the needs of various projects. They provide customized solutions for their clients with a diverse product portfolio.
- Keeping Up with Technological Advancements: These companies stay up-to-date with manufacturing processes and material technologies, ensuring they meet quality standards and follow the latest design trends.
- Project Management: Effective management of all phases, from understanding customer needs to design and installation, ensures the success of the entire project.
Üçgen Alüminyum stands out as a composite cladding company based in Turkey, specializing in the production and installation of aluminum composite panels. Some of the values offered by Üçgen Alüminyum include:
- Customized Solutions: Üçgen Alüminyum provides tailored solutions to meet the unique aesthetic and functional requirements of each project.
- Quality Focus: The company aims to deliver durable and aesthetic solutions by using high-quality materials.
- Customer Satisfaction: With a customer-oriented approach, the company ensures effective communication and collaboration throughout the projects.
- Diverse Project Expertise: Üçgen Alüminyum is involved in a wide range of projects, including commercial buildings, residential developments, shopping centers, and industrial facilities.
Composite Exterior Cladding m² Prices
Composite exterior cladding m² prices and composite panel unit prices can vary depending on several factors. These include project size, material quality, color and pattern options, installation labor, and building height. Additionally, geographic location, market demand, and economic conditions also influence prices.
As a general idea, the m² price of aluminum composite panels typically ranges from $40 to $120 per square meter. However, these prices do not only include the cost of the panels but also encompass installation labor, substructure materials, transportation, and setup costs.
When determining prices, it is essential to consider the following factors:
- Material Selection: The quality, colors, and patterns of the panels affect the price. Custom colors or patterns often incur higher costs.
- Project Size: Larger projects often benefit from discounts on m² pricing, while smaller projects may face higher rates.
- Installation Labor: Installation labor and substructure costs usually constitute a significant portion of the total project cost.
- Location: Geographic location impacts transportation and labor costs for materials.
- Project Complexity: Special cuts, intricate details, or challenging installation requirements can increase costs.
- Economic Conditions: Market demand, supply and demand dynamics, and material costs are influenced by economic conditions.
For this reason, it is crucial to consider the specific needs of your project and local conditions when determining composite exterior cladding prices. Requesting a quote from a professional company tailored to your project is the best approach. For support with your project, contact us.
How to Design Aluminum Composite Curtain Walls?
- Project Analysis and Goal Setting: The first step is to define the type, purpose, and goals of your project. What kind of building is the curtain wall being designed for? Is aesthetics, energy efficiency, or durability the priority? This analysis forms the foundation of the design process.
- Defining Aesthetic and Functional Requirements: Determine how the facade should look and what functions it needs to serve. Define aesthetic details such as color, pattern, texture, and light effects.
- Material Selection: Choose the color, texture, and quality of the aluminum composite panels. It is important to select panels that complement the building’s style and surrounding environment.
- Panel Distribution and Layout: Plan how the panels will be placed and mounted. You can create creative patterns by combining different panels.
- Detailing: Design the details for corners, edges, door and window openings. These details ensure aesthetic and functional cohesion in the facade.
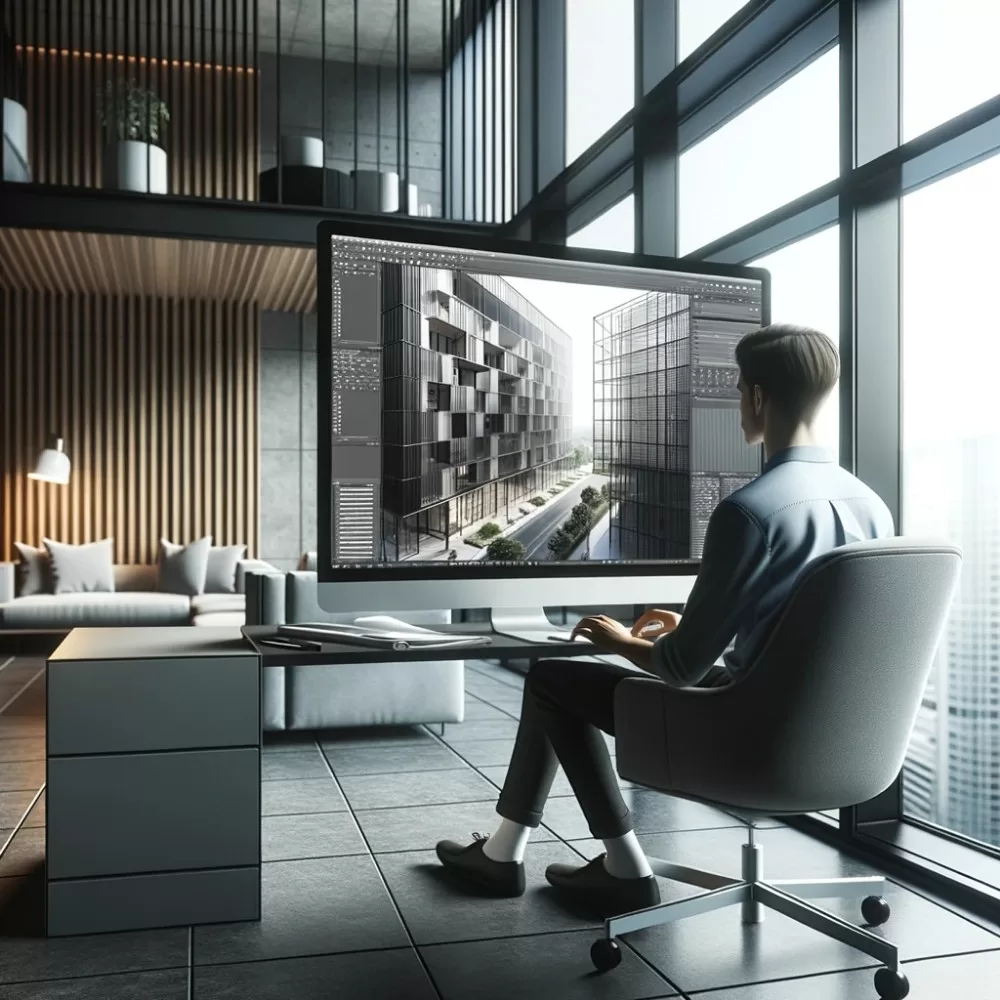
- Considering Building Features: The structure, height, and orientation of the building affect the design. Keep in mind that the facade will be exposed to sun, wind, and other environmental factors.
- Safety and Fire Precautions: Ensure safety and fire precautions are included in the design process. Consider factors such as fire resistance and emergency exit points.
- Functional Elements: Enhance the facade design with functional elements. For example, you can create areas between panels that allow for ventilation or light passage.
- Cost and Budget: Keep the project budget in mind while designing. The cost of the design is related to material selections, installation labor, and other factors.
- 3D Modeling and Visualization: Use professional design software for 3D modeling and visualization. This is important for seeing your design more clearly and realistically.
Aluminum composite curtain wall design becomes more effective with teamwork and an experienced design team. Additionally, ensure the design is accurately implemented during the manufacturing and installation phases. For support with your project, contact us.
How Durable Are Aluminum Composite Curtain Walls?
Aluminum composite curtain walls are a cladding material that offers several durability advantages. Their durability depends on material quality, installation method, environmental conditions, and maintenance practices. Generally, aluminum composite curtain walls have the following durability features:
- Weather Resistance: Aluminum composite panels are resistant to external factors such as sunlight, wind, rain, and snow. Their surface is designed to prevent fading, cracking, or blistering.
- Rust Resistance: Aluminum panels do not rust, even when exposed to moisture and rain, making them highly durable over time.
- Low Maintenance Requirements: These panels are popular for their low maintenance needs. Regular cleaning and periodic care are typically sufficient to maintain their condition.
- Aesthetic Longevity: The colors and patterns of aluminum composite panels do not fade or degrade over time, ensuring that facades remain visually appealing for years.
- Fire Resistance: Most aluminum composite panels have fire-retardant properties, though the level of fire resistance varies depending on the material type and core composition.
- Flexibility and Sustainability: Aluminum composite panels are lightweight and flexible, allowing them to adapt to building movements and making them a sustainable choice.
- Impact Resistance: High-quality aluminum composite panels are resistant to impacts and scratches.
However, factors such as material quality, adherence to manufacturing standards, installation quality, and proper maintenance routines should be considered for durability. For an accurate assessment of the expected lifespan of aluminum composite curtain walls, it is important to conduct a project-specific evaluation and seek expert advice.
How to Clean Aluminum Composite Curtain Wall?
Cleaning aluminum composite curtain walls is essential for maintaining their aesthetic appearance and durability. Here are the steps for cleaning aluminum composite curtain walls:
- Surface Inspection: Before starting the cleaning process, thoroughly observe the surface and, if necessary, follow the steps below.
- Dust and Dirt Removal: Use a soft brush or cloth to remove light dirt and dust. Avoid applying excessive pressure, as it may scratch the surface.
- Preparing Cleaning Solution: Mix water with a mild cleaning agent (e.g., soap or a specific cleaning solution) to create a gentle cleaning solution. Avoid using aggressive chemicals, as they can damage the surface.
- Cleaning Process: Place the cleaning solution in a bucket of water. Use a clean cloth or a soft sponge to apply the solution to the surface. Gently wipe the surface with light pressure, avoiding scrubbing.
- Stain Removal: For tough stains, use appropriate cleaning products. However, it’s a good idea to test them on a small, inconspicuous area first.
- Rinsing: Rinse the surface with clean water to remove the cleaning solution. Apply clean water to the surface and wipe it down, then dry it with a cloth.
- Drying: Use a clean, soft cloth or sponge to dry the surface. Ensure the surface is thoroughly dried to prevent water spots.
- Periodic Cleaning: Regularly clean the facade to maintain its condition. It is generally recommended to perform periodic cleaning once a year or more frequently as needed.
Be cautious during the cleaning process and avoid using abrasive materials or hard brushes, as these may scratch the surface. Additionally, select cleaning products and methods based on the manufacturer’s recommendations.